AIM Photonics Will Give Already-Exploding AI/ML Shot In The Arm
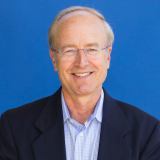
The United States is winning a global battle for domination in integrated photonics, thanks in part to a Manufacturing USA innovation institute that the Obama administration stood up in 2014. And manufacturers embracing artificial intelligence and machine learning will benefit greatly. That is according to John Bowers, acting CEO of the Manufacturing USA innovation institute called AIM Photonics.
“The chips that Intel and Broadcom announced recently are 25-terabyte-per-second chips, so that’s 25,000 gigabytes/second, or 25 million megabytes/second,” he said. “That’s how much data each of them processes. It lets your networks just keep getting faster and more complex, so they can handle more data.
“Where that really matters is for things that involve AI and machine learning (ML). They take huge amounts of computing capacity,” he said. “And for data centers to be able to handle that, they need this much higher capacity,” which is partly due to the fact that capacity of an optical fiber is 1,000 times that of an electrical wire, and that the signal loss in fiber optics is “about 1,000 times lower than electrical wires.”
To get to the point of building terabyte chips alongside industry partners like Intel and Broadcom, AIM Photonics has played a leading role in three dramatic shifts in the making of microchips.
First, researchers at U.C. Santa Barbara (UCSB), an AIM Photonics member, working with Intel made history when they “developed the technology to integrate lasers onto photonic integrated circuits (PICs),” Bowers said. UCSB then teamed up with Intel to integrate lasers onto PICs. “Intel is now making photonic integrated circuits.”
Second, the institute is challenging the norm of making PICs using materials like indium phosphide or gallium arsenide or gallium nitride. “They’re so-called III-V materials, meaning column three, column five of the periodic table. And those materials are very efficient light emitters,” he said.
“The photonic integrated circuit industry has been entirely based on indium phosphide and these III-V materials” but researchers at AIM Photonics are leading the switch to silicon, he added. To be sure, there are “big efforts” to do the same—which means making photonic integrated circuits in a fully automated CMOS (complementary metal oxide semiconductor) foundry—in Asia and Europe, including at AI specialist IMEC, Bowers said. “It’s a global race. And I would say Intel is leading the commercial end of it, and AIM is leading the research end of it.”
One of AIM’s central goals is “to make photonic integrated circuits the same way electronic-integrated circuits are made,” he said.
On this front, Taiwan Semiconductor Manufacturing Co is nibbling at Intel’s heels.
It is exactly the sort of situation U.S. President Joe Biden spoke to in 2014 as he announced the formation of AIM Photonics: Then-Vice President Biden noted that the U.S. used to lead in photonics and telecommunications—but that after 2000 there was a big collapse and much of the manufacturing for photonics got sent to Asia because it was very labor-intensive, Bowers recalled. “The decision was made to have an institute in integrated photonic circuits” in order to leapfrog similar efforts around the world.
“We now have a photonic design capability that is No. 1 in the world,” he asserted. “The whole effort has been transformative.”
Intel is now making photonic integrated circuits. “I would say, in terms of doing this on silicon, they’re the world leader,” Bowers said. Other than Intel, “no one really integrates all the photonic elements on silicon, including the laser,” he added. “The laser is typically off chip because integrating it is a difficult problem to solve.
AIM Photonics has what he called “a major new research effort” to integrate all the photonic elements on silicon. It is a collaboration between UCSB, a company called Analog Photonics and SUNY (State University of New York), which hosts the institute. The PICs are made in a CMOS-foundry-like R&D center called Albany Nanotech, and after the chip wafers are diced up, the chips are packaged in Rochester. Analog Photonics leads the photonic design kit (PDK). UCSB’s Institute for Energy Efficiency is the West Coast headquarters of AIM Photonics. The third dramatic microchip-making shift in which AIM Photonics has figured prominently is in 3D-bonding optics with electronics. “That means that the input and the output on electronic chips can now be optical”—which increases the speed and capacity of data transfer and reduces the power required to do so, Bowers said.
“Before long, your processor in your computer will be communicating with other chips in your computer optically,” he added. “That is a huge revolution. What that really drives is silicon photonics. Because now you need to be doing everything on silicon since the chips all need to have the same expansion coefficient.”
The imminent switch to photonic communications will mean products as ubiquitous as the personal computer will change dramatically.
“The optical connection is going to go all the way to the processor in your computer,” Bowers said. “Today, you connect up to this electrical Ethernet cable or wi-fi connection. But in the future, inside your computer, it’s going to be optical. And that’s as big a revolution as the whole Internet was: Internet and fiber optics together. That would have never happened unless we had high-capacity connections.”
When the chip is co-packaged, “the data going in and out of that chip” will no longer be electrical, he said. “Today, every processor chip, memory chip, switching chip, FPGA chip you buy, all have electronic I/O, input and output, and that is going to change.”
Funding comes from all corners
Of course, all of these accomplishments involve spending big.
The institute got started with $110 million from the federal government, along with $250 million from New York State. “And then California matched, and Massachusetts matched, and lots of companies signed up for multi-million dollar involvement—Cisco, IBM and a bunch of other companies,” Bowers said.
DARPA’s LUMOS program—whose goal is to integrate lasers with photonic integrated circuits—brought in $19 million. And an Air Force Research Laboratory program—with the goal of laser integration on silicon—is adding more than $10 million to AIM’s effort.
“Now we’re moving to what we call ‘AIM 2.0.’ The original federal funding is running out. But there is still a substantial amount of New York State funding,” and the institute is still signing up companies and universities and institutions for support, Bowers said.
“It is a self-sustaining model,” he said, but AIM Photonics 2.0 is also “looking for additional federal money” some of which is likely to come this year.
To become self-sustaining, AIM needs “to keep getting new research grants, keep looking for funding and then have enough industrial companies signed up to run wafers through our facilities,” Bowers said. “If we have enough flow of wafers, that will pay for itself and be completely sustainable. That’s the goal.”
Impact to be felt first in automotive, medical
Two manufacturing market segments bound to be profoundly impacted by AIM’s work are automotive and medical, which are becoming more dependent on AI and machine learning by the day.
Lidars (shorthand for light detection and ranging) and gyroscopes will benefit, Bowers said. “That’s for self-driving cars: the ability to see 300 meters ahead and accurately be able to figure out if something is a tumble weed or a child. That’s a big application of optics, and something that’s really well suited for silicon photonics.”
Sensors used in, for example, COVID-19 detection are also on AIM’s radar in a big way.
“One of the big wins for AIM is the research on COVID detection that’s been going on in Ben Miller’s group at the University of Rochester” he said.
Nathaniel Cady, executive director at the SUNY Applied Materials Research Institute, said the optical implementation of AI could and should greatly reduce microchip power requirements.
That means data will move much faster.
“The automotive applications are already here, and medical applications are very near term—as in within the year,” he said.
Then, within five to 10 years, manufacturers of all stripes that employ edge-based computing—“anything that’s deployed that’s not in a server room”—will benefit, Cady said.
Photonic integrated circuits made on silicon will mean high volume and extremely low cost for manufacturers.
“In Intel’s case, in just a year or two, they brought silicon PIC-based transceivers up from zero to millions of transceivers per year, which is a billion-dollar market for them,” Bowers said. “And once we get to co-packaged optics, the volume of silicon PICs becomes even larger. Switching chips, processors, memory chips will all have silicon PICs.”
By Brett Brune
Editor in Chief
Smart Manufacturing magazine